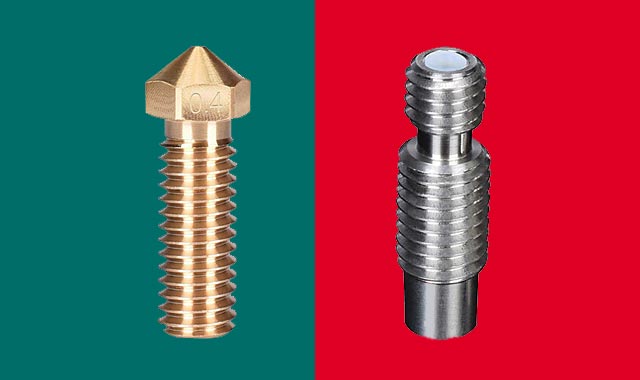
Когда мы только начинали заниматься 3D печатью, то собрали на базе системы Н-бот, корпуса от ZAV и линейных направляющих простой принтер со столом 200х200 мм. Цилиндрические направляющие мы использовать не стали потому, что скорость печати на них ниже и провис тяжёлой печатающей головки больше. Провис головки может создать проблемы, когда сопло задевает за деталь и это может привести к отрыву от стола тонких поддержек.
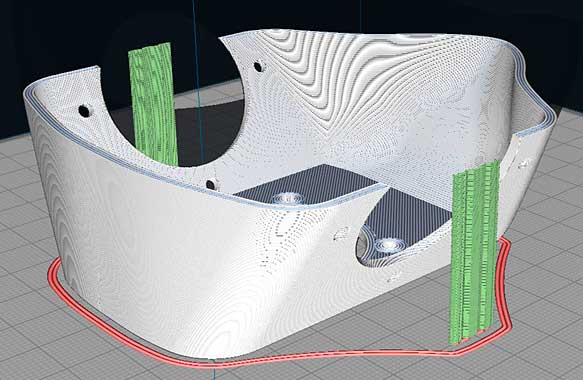
Также может случиться еще большая неприятность, когда сопло зацепится за деталь и из-за этого ремень перескочит через шкив на несколько зубцов и тогда получится вот такая деталь со смещением:
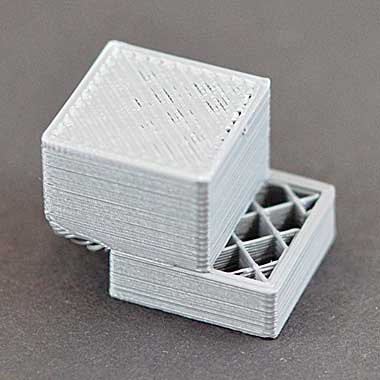
В своём принтере мы изначально мы использовали самый простой экструдер
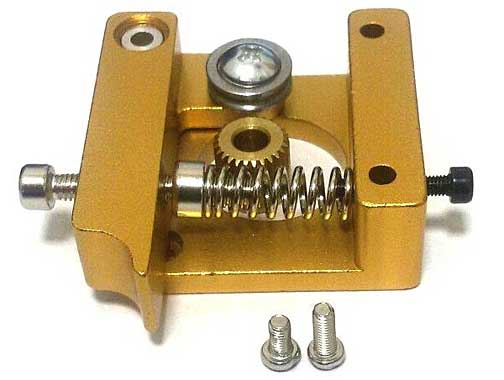
и головку под боуден-систему. В этом варианте филамент подается через экструдер в длинную трубку, на конце которой находится печатающая головка. Преимуществом такого решения является облегчение печатающей головки за счёт того, что двигатель и толкающий экструдер располагаются на корпусе принтера. Но данная система имеет определенные минусы — не очень качественно работает откат (отвод филамента обратно при перемещении головы) и не идеально производится подача пластика в сопло потому, что между толкающим экструдером и соплом находится значительное расстояние по трубке (около 35 см).
При печати легкообрабатываемыми пластиками, такими как ABS, HIPS или PLA, это не так страшно, потому что образуемые от неточной работы отката тонкие волоски и наплывы филамента в местах начала печати, можно легко сошкурить или срезать. А вот при печати более прочным пластиком типа PET-G подобные неточности уже доставляют серьезные проблемы. Удалить их уже не так просто, а в некоторых местах, к примеру внутри сложной детали, так и вообще крайне проблематично.
Вот такие безобразия образуются из-за того, что пластик не полностью убирается и частично вытекает из сопла. В месте начала печати то, что успело вытечь, налипает на деталь. Это один из недостатков печати боуден-системой.
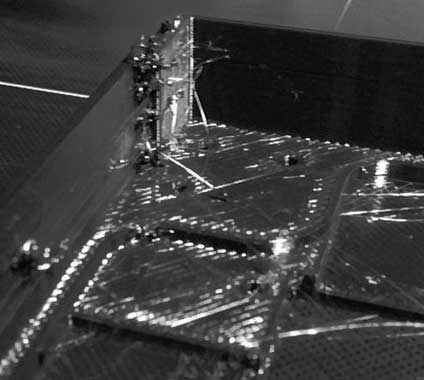
Создание директ-системы печати
Как только мы поняли, что для нашей работы нужен именно PET-G, то встал вопрос о необходимости переделки нашего 3D принтера под директ-систему, в которой экструдер располагается непосредственно на печатной головке для максимального сокращения расстояния между подающим механизмом и соплом. Чем это расстояние меньше, тем точнее будет печать.
Однако, если обычный экструдер со стандартным для принтеров шаговым двигателем разместить на печатающей головке, то из-за тяжести этой конструкции головку по инерции будет «заносить» при резком изменении направления печати. Соответственно, углы деталей будут с «выносами». А значит либо придется снижать скорость печати, либо уменьшать вес конструкции головки. И сделать это можно только за счет установки более лёгкого шагового двигателя.
Но чем легче двигатель, тем он слабее. У него просто может не хватить мощности провернуть вал, если сопротивление будет большим, а на высоких скоростях печати подача должна идти достаточно интенсивно. Решить эту проблему можно увеличением силы тока, поступающего через драйвер двигателя, но и тут есть проблема — двигатель при этом начинает весьма сильно греться.
Для решения всего этого набора задач умные люди придумали экструдер Titan, работающий по принципу редуктора, что как раз и позволяет использовать тонкий и легкий двигатель, да и точность подачи филамента значительно улучшает.
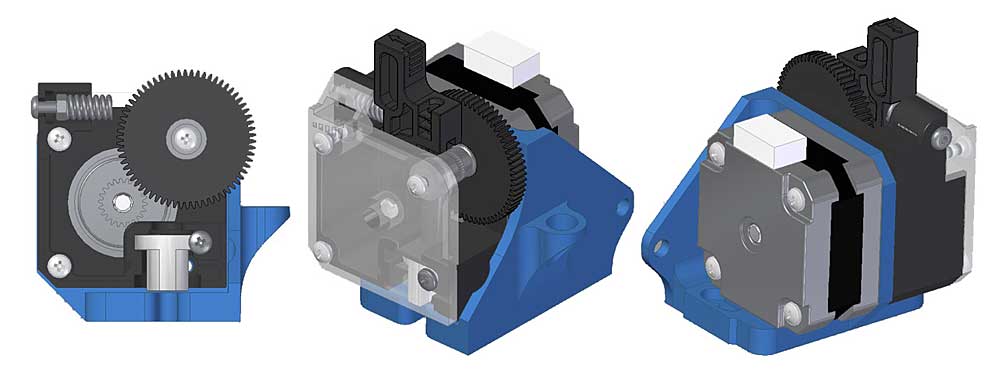
Мы разработали посадочное гнездо, закрепили в нем на головке Titan с легким двигателем и с этого момента работа с принтером стала приносить настоящее удовольствие. Точность печати просто отличная, а благодаря линейным направляющим и скорость печати на высоте. В целом, система Н-бот оказалась весьма надежной.
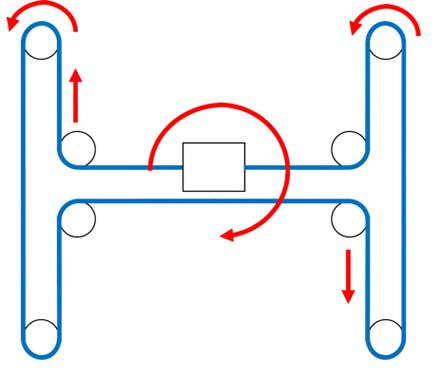
Правда и размер области печати на данном принтере небольшой. Для столов размером под 400х400 мм и больше, нужна уже другая система Core XY. Она компенсирует перекос длинной оси Х при передвижении (при малых габаритах этот перекос практически не влияет на печать).
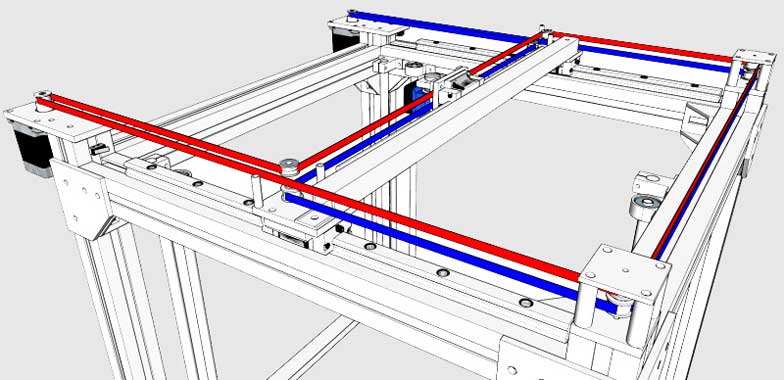
TPU филамент
Затем к нам в руки попал TPU филамент (силиконовый, как резинка) от FD Plast и обнаружилась еще одна проблема: этот филамент требует практически идеальных условий для собственного протекания от экструдера до сопла. Но у экструдера Titan вот в этом месте
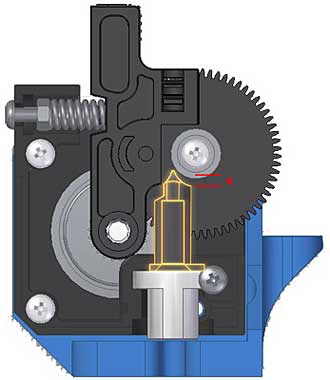
присутствует небольшой зазор в 2 мм и филамент постоянно вываливался прямо из под подающей шестерни наружу. Мы переделали эту деталь таким образом, чтобы зазор пропал, напечатали ее и TPU перестал вываливаться наружу. Правда попутно пришлось поменять и термокуб на E3D V6
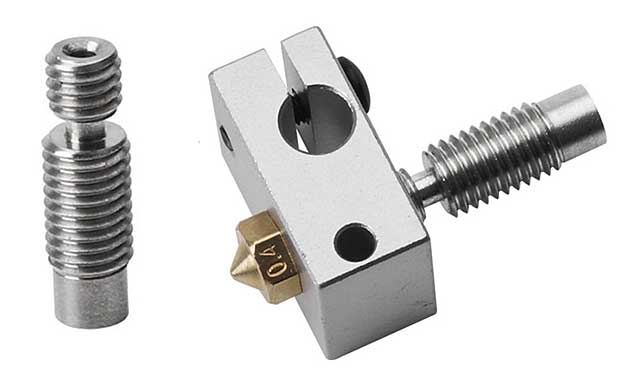
потому что раньше у нас стоял E3D Volcano
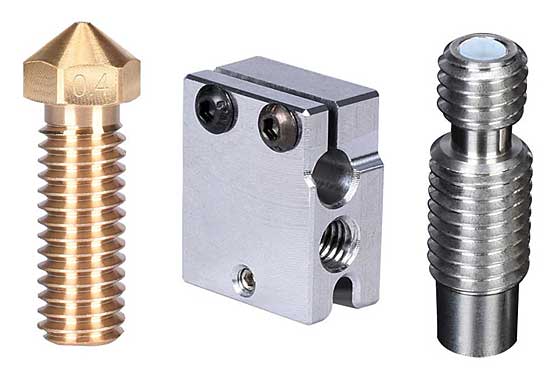
который весьма длинный, что для TPU также нежелательно, да и сопла для него стоят дороже, а из строя выходят также регулярно. Для работы с TPU лучше иметь отдельное сопло, чтобы не забивать его другим пластиком. У того же PET-G минимальная температуры 230 °C, а у TPU максимальная 220 °C. Однако часто менять сопла тоже не стоит, потому, что у термокуба V6 очень слабая резьба. Как показала практика, для TPU лучше вообще иметь отдельный принтер, который будет идеально настроен под него.
TPU — это замечательный и очень полезный в хозяйстве материал. К примеру, прокладка износилась в кране — если есть подходящий принтер и понимание как сделать 3D модель, то это вообще не проблема. Можно делать всякие амортизаторы и т. п., но есть некоторые проблемы:
- Поддержки из него делать крайне сложно, соответственно и модели надо проектировать соответствующие.
- Нависающие части деталей печатать также проблематично, потому что пластик как резинка и под собственным весом просто может провиснуть. Из-за этого печать уже продолжается по воздуху, так как даже если деталь провиснет на 0,3 мм, то нитке филамента цепляться будет уже сложно и, учитывая текучесть данного филамента, он просто будет скапливаться на конце сопла.
Наши планы
Помимо описываемого, у нас в лаборатории начали появляться и другие принтеры. В основном это были Эникубик-и. Почти все время их использования мы не прекращали с ними возиться. Постоянно что-то было не так, а всё это время наш первый принтер работал и работал чётко и без капризов выполняя свою работу. У нас сложилась уверенность, что если нужно напечатать что-то сложное и важное, то наш самодельный ZAV не подведет. Прямо как в к/ф «Движение вверх»:
— …если дело плохо, просто отдай мяч Сереге.
Натуральный автомат Калашникова 3D печати — конструктивно очень простой и потому всегда надежный. Но у нас есть идеи по его модернизации:
- улучшение удобства использования
- упрощения доступа к деталям принтера при ремонте
- добавление визуального контроля за 3D печатью
- автоматизация печати там, где это разумно
У нас есть идея разработки своего принтера с большим столом. В принципе, собрать надежный принтер оказывается не так уж сложно. Но есть один нюанс — при ширине стола более 20 см начинают возникать проблемы, например, даже зеркало имеет не идеально ровную поверхность да и нагревательный стол может при нагреве провисать. При высоте слоя печати от 0,2 до 0,4 мм подобный провис начинает создавать серьезные проблемы.
Но мы полны оптимизма и творческих идей по созданию собственного идеального 3D принтера и будем знакомить вас с нашими успехами в этом блоге!